

Screen
This equipment is usually placed after each crushing step and controls the crushed materials. In the crushing plants, a screen is used to classify particles from coarse to fine. The most important parameter of Screen spring is the Screen orifice, which varies according to the needs and desired stage.

The efficiency of plants plays an important role in the overall efficiency of the plants and other crushing equipment, because if plants is disturbed, it will be disrupted and:
1.Some of the finer minerals from screen spring will be re-crushed
2.Some of the coarser materials are transferred from the Screen spring to the next stage.
Screen applications
In general, screens are used to categorize and classify materials. Screens are divided into several categories based on the conditions and dimensions of minerals. According to the need and wide dimensions of mineral materials, they design the screens as one or more floors, they are able to classify a wide range of material (from the size of 700 mm to 75 microns-high frequency).
Application of screens in different industries
Mineral processing industries
Chemical industry
Construction industry
Sand mines
Food industry
Agriculture industry
The driving force of screens is divided into several parts depending on the type of mineral, capacity and process stage.
Shaft and crank
Engine unbalance
Exciter
Type of equipment
There are different types of sanders depending on the purpose of the sanding process and the different stages of the process.
- Scalping Screen
To separate coarse materials
- Sizing Screen
To produce specific sizing from the mixture of input materials
- Washing Screen
Including spraying water on the materials, to wash them or help sizing
- Dewatering Screen
To separate water from materials (with a negative slope to facilitate the dewatering process)
To separate small or waste materials from materials that have already been processed
The freezing process is done in two ways, wet and dry, depending on the next steps of the process.
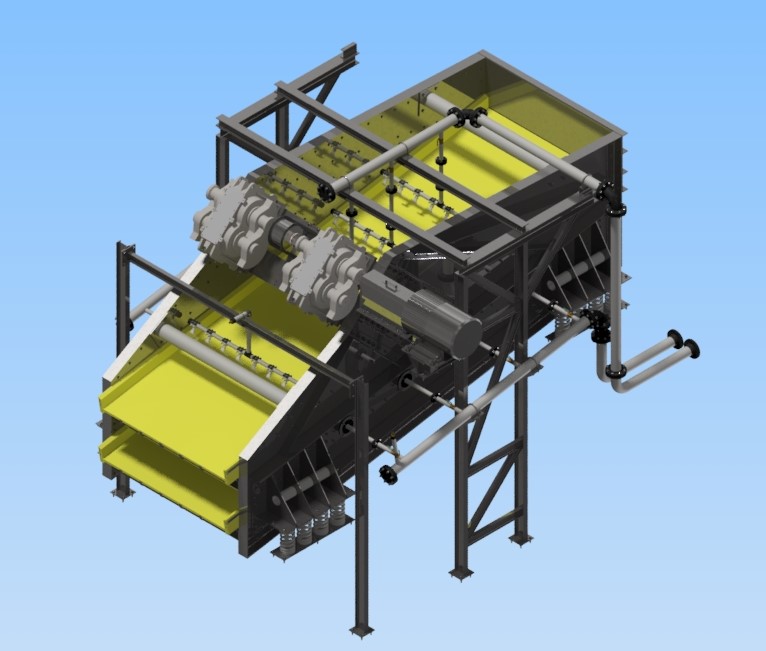
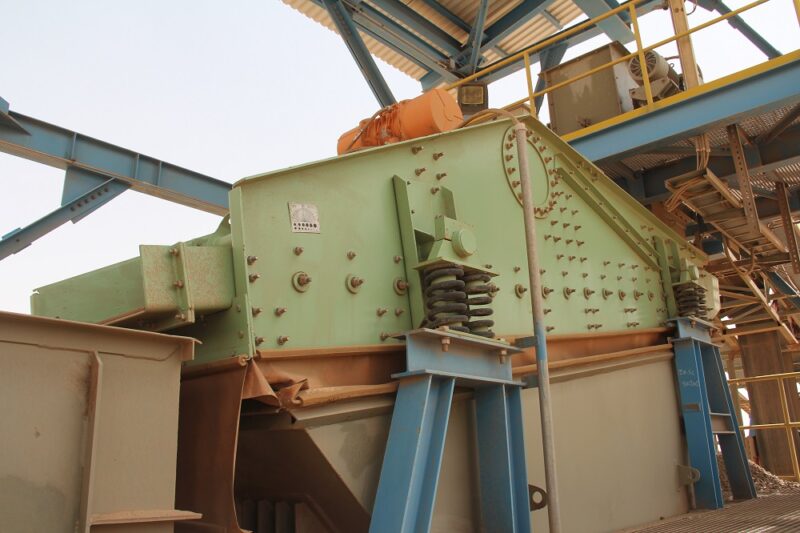
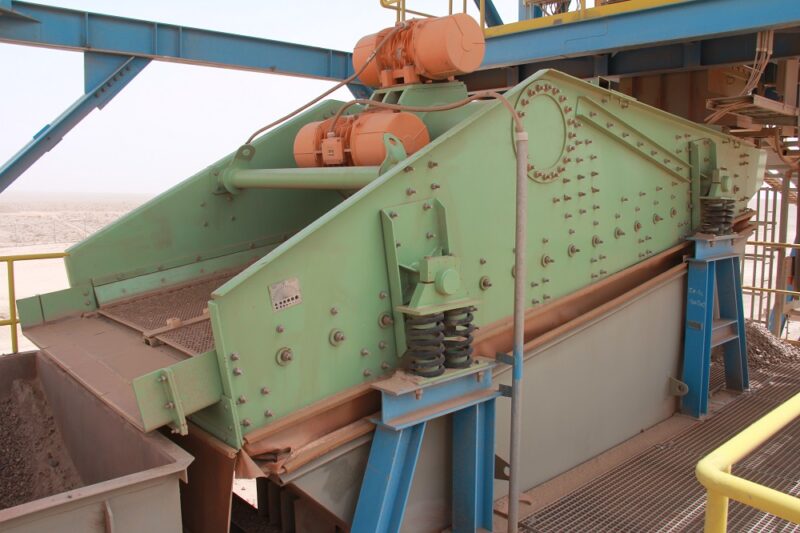
The most common industrial screens
-
Grizzly drills (they are considered primary drills and are effective for materials with very large dimensions of 350 mm and dry)
-
Vibrating screens (it is the most widely used type of screens, which has a wide range of particles from 75 microns to 350 mm and is used in both dry and wet types)
FMS has been operating since 1992 in the field of design and manufacture of magnetics by using the latest equipment, test equipment and having experienced experts. See also 2020.
With more than 30 years of experience, this company is able to manufacture all types of shunts in different dimensions and capacities for various processing factories and mines. Also, this company has designed and built the largest screen in the country with dimensions of 7.2 x 9. It is worth noting that this company has the ability to manufacture 850 degree temperature resistant furnaces for iron smelting (DIR) and baked pellets industries.